Building Better Ways of Working
Every Challenge is a Chance to Prove Our Skills
Our job goes beyond delivering exceptional work in the field safely. As your partner, we strive to answer your challenge with innovative solutions that maximize quality output, minimize safety risks, and modernize projects. Our innovative approach to answering your toughest challenges delivers better work, faster and more cost-effectively.
We bring experience, perspective, and technology to every one of your projects so we can deliver work more efficiently and help you build a better business. Our expertise and strong union relationships enable us to scale projects from small to mega and everything in between.
Powered by Quality & Quantity
At Enerfab, people are our biggest asset. We proudly support craft labor with more than 4.62 million labor hours in 2024 and more than 18 million over the last 5 years.
Our teams are carefully trained and nurtured to be built for the challenge. As the #1 craft employer under the National Maintenance Agreement, we’re privileged to have access to and the loyalty of some of the most capable craftworkers in their fields.
Our strong union relationships coupled with our extensive industry legislative knowledge of Project Labor Agreements (“PLA”) create more efficient speed to market. Our ability to tap into a diverse talent pool provides rapid scalability for projects of all sizes.
Our focus is delivering predictable results
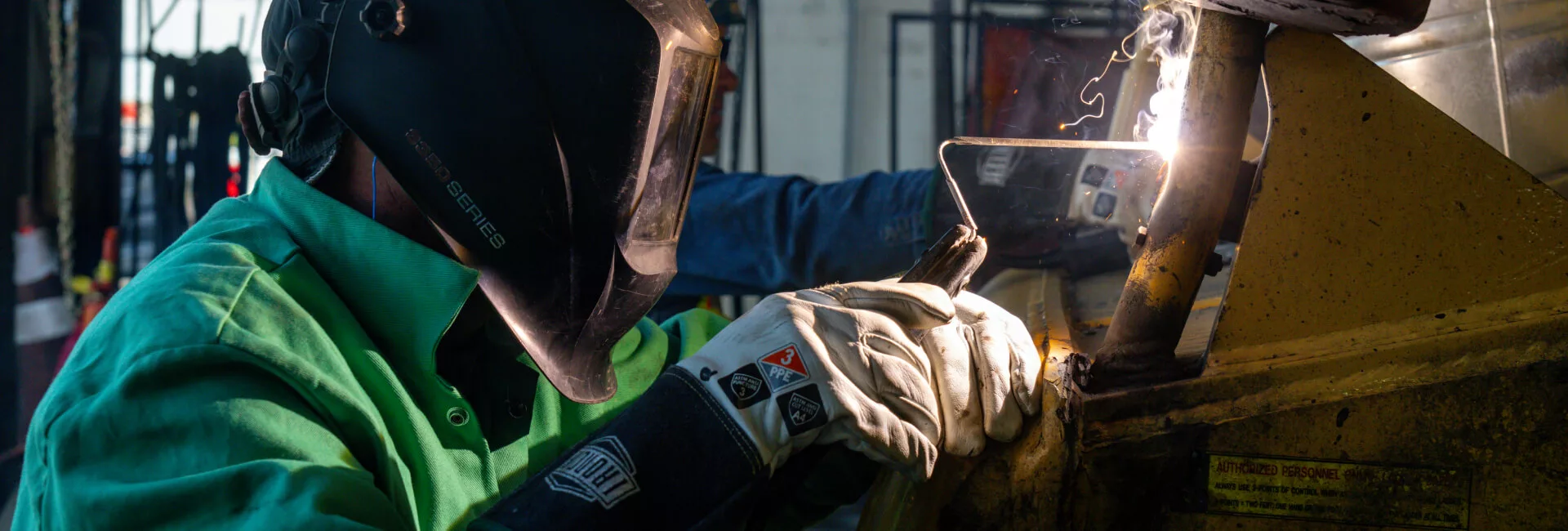
Quality
Delivering excellence through execution is our mission. It’s a commitment to a finished product that always meets or exceeds our customers’ expectations.
Our Quality is Our Customers' Safety
The impact of our work stretches far beyond the project details and completed tasks. The products we fabricate and our work in the field become the everyday workplace for your team. Quality craftsmanship and safety matter most, so we are committed to delivering excellence.
Quality Standards & Certification
Our quality program is based on and audited using ASME guidelines. Enerfab craftworkers are certified in more than 1,500 ASME Section IX weld procedures.
-
- U – Unfired Pressure Vessel: We can design, fabricate, inspect, and test unfired pressure vessels. Pressure vessels bearing the U stamp meet the requirements of a pressure vessel described in Section VIII Division 1 of the Boiler and Pressure Vessel Code (BPVC).
- U2 – Division 2 Pressure Vessels: Pressure vessels bearing this stamp meet the requirements for pressure vessels described in Section VIII Division 2 of the BPVC. This division of the standard provides rules alternative to those of the U stamp and certifies us to design, fabricate, inspect, and test these pressure vessels.
- S – Power Boilers: This enables us to fabricate ASME-compliant pressure-retaining parts, power boilers, and power piping (B31.1). Like the U and U2 stamps, a quality assurance program that meets the standards outlined in the BPVC is required.
- PP – Pressure Piping: We can design, fabricate, and install piping systems, components, and appurtenances for power plants, pressurizing equipment, and other industrial applications.
-
- NB – Registration of Boilers & Pressure Vessels: This indicates that a pressure vessel or boiler has been constructed and inspected according to the ASME BPVC and ensures that it meets stringent safety and quality standards.
- R – Metallic Repairs & Alterations (Shop & Field): Awarded by the National Board of Boiler and Pressure Vessel Inspectors (NBBI), this enables us to repair and alter pressure-retaining equipment, including pressure vessels and boilers.
-
- AISC
- API 650/620
- ASNT (SNT-TC-1A)
- ASTM, ANSI, ASM, ASCE, NSPE
- AWWA
- AWS
- Material Technology Institute (MTI)
- NACE
- SSPC
- Steel Tank Institute (STI)/Steel Plate Fabricators Association (SPFA)
- The Edison Welding Institute (EWI)
-
Over 1,500 ASME-qualified procedures including:
- Stainless/Duplex Steel – P6 to P8/P10H
- Nickel Alloys – P41 to P47
- Carbon/Alloy Steel – P1 to P5/P9 to P15E
- Clad – All Combinations
- Aluminum Alloys – P21 to P25
- Copper Alloys – P31 to P35
-
- Austenitic
- Superaustenitic/Nickel
- Duplex
- Chrome-Moly
- Carbon Steel
- Combinations of Clad Materials
Quality Testing
In addition to quality guidelines and welding procedures, our quality engineers also utilize a wide variety of quality testing procedures.
NDT (ASME Section V)
- Digital Radiography (DR-RT)
- Computed Radiography (CR-RT)
- Liquid Penetrant Testing (PT)
- Magnetic Particle Testing (MT)
- Ultrasonic Testing – Thickness (UT)
- Visual Testing (VT)
- Helium Leak Detection (LT)
Additional Testing
- Boroscopic Visual Inspection
- 3D Laser Scanning
- Positive Material Identification (PMI)
- Wet & Dry Film Thickness
- Holiday Spark Testing
- Hydrostatic Testing
- Pneumatic Testing
- Clad Thickness Testing
- Hardness Testing
- Guided & Testing
- Ferrite Testing
- Surface Profile Testing
- Thermal Infrared Testing
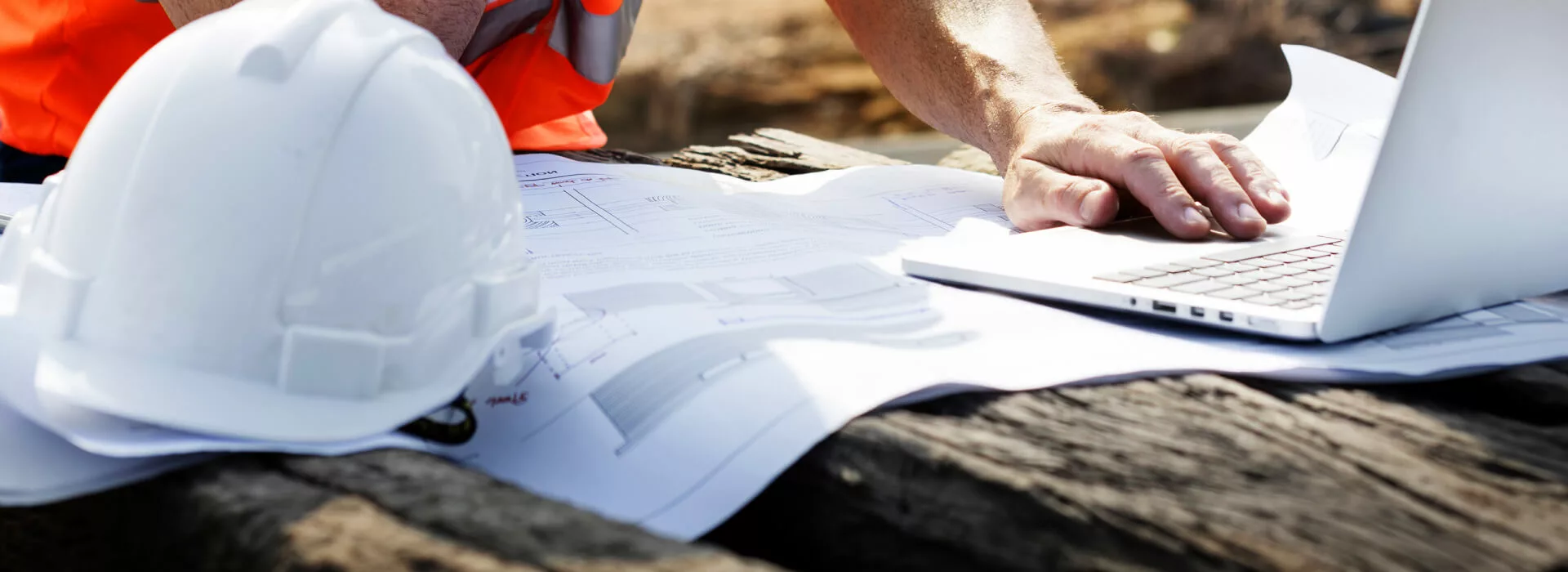
Customer Experience
Project Planning & Execution
Our internal project management process aims to eliminate quality issues and deliver a best-in-class result. Your designated project team carefully orchestrates your project through each phase of this proprietary process, which includes the following:
-
Opening lines of communication with the customers to discuss the project scope and requirements to ensure a smarter build.
-
Building out the project scope (what services are needed) and a breakdown of the cost of the projects.
-
Determining how to best attack the project based on the project needs and schedule to deliver predictable results.
-
Executing the project within the scheduled parameters and costs.
-
Closing out the project with each customer by delivering on project goals, measuring satisfaction, and filling out the necessary closing documents.
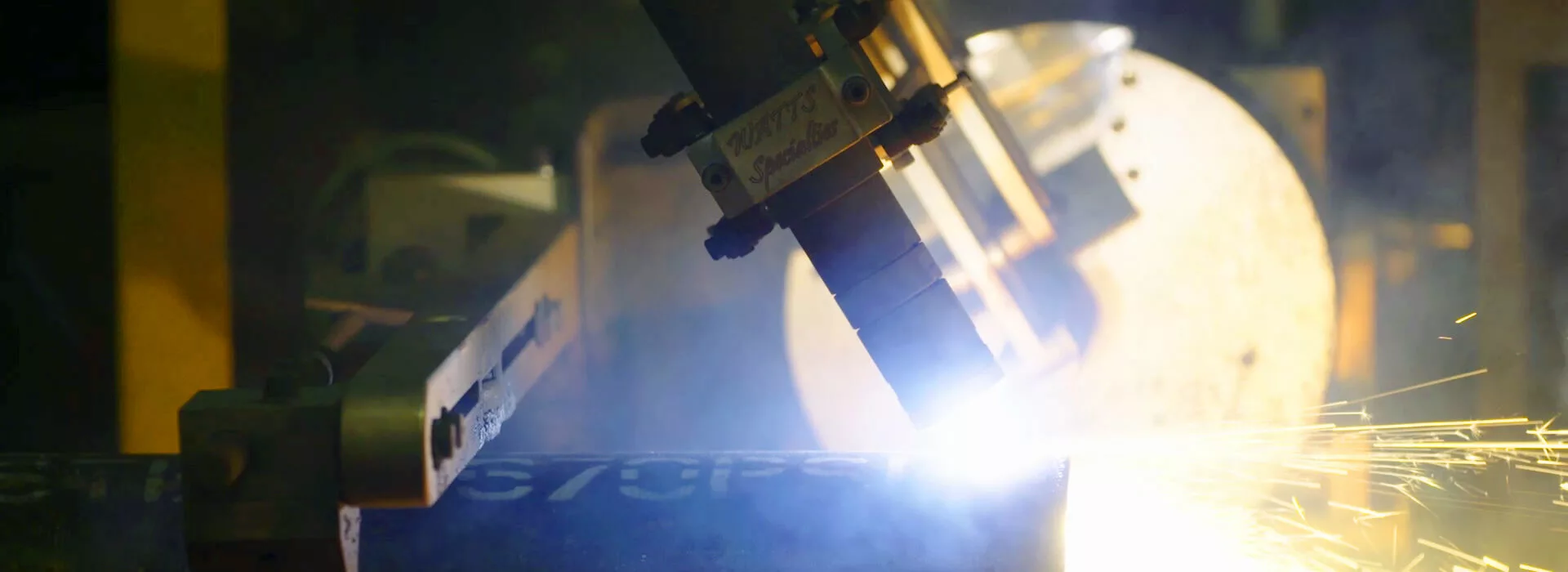
Technology & Innovation
Technology & Innovation
As our customers and markets grow, we strive to stay ahead by introducing new technology, innovation, and unique ways of working that create safer, more efficient projects, job sites, and shops. The technologies below just scratch the surface of our innovative approach to your projects.
-
Our innovative Viewfab (“VF”) project tracking enables customers to see their project’s status in real-time, helping them better track delivery and manage on-site project schedules. This client portal gives our customers complete access to project updates during and throughout the fabrication process. Once they log in, customers can access their projects and see every aspect of the project’s development.
-
At Enerfab, we recognize that the job isn’t done until it arrives safely at your job site or facility.
We leverage our shop capabilities, in-house digital drawing and document display kiosks, and partners to deliver your project and meet your speed-to-market goals.
-
As a vertically integrated company, we leverage our shop and field capabilities to control the project schedule from concept to completion.
-
Through our affiliate companies, long-standing vendor relationships, and diverse supplier networks, we offer expanded scopes and turnkey solutions.
As a result, we are your single source provider, enabling more control over project timelines and delivery.
-
Production begins on day one when planning, engineering, and execution coincide to meet your tight turnaround window. We work alongside you every step of the way to ensure that safety and quality are never sacrificed even with accelerated timelines.
-
Scanning technology quickly captures over 3 million data points on facility structures and systems to produce near-perfect 3D models.
- Scanning – Digital scanning shortens shutdowns and mitigates safety risks while capturing data much quicker than traditional measuring processes.
- Engineering & Design – Once captured, scans enable accurate design review and estimates before construction to optimize the constructability of even the most complex projects.
- Project Control – Throughout the life of the project, 3D scans aid in verifying equipment installation, tracking project status, and ultimately closing the communication loop with more consistent data.
- Modular Application – By leveraging these data points, the scanning helps us be sure that your modules fit precisely each time.
-
Robotic welding has enabled the craftworkers in our fabrication shops to increase throughput without sacrificing quality. These robots support our skilled welders while shortening production time and maximizing available fabrication space.
- Cold Wire GTAW Welding: With the addition of automatic wire feed, deposition rates can approach that of GMAW while realizing GTAW quality.
- Narrow Groove Welding: This welding technique is used on heavy-wall vessels to create the best metallurgical condition by minimizing heat-affected zones and reducing angular distortion. It also decreases the quantity of consumables necessary to complete the joint and lessens weld durations. A good example would be the manufacture of CrMo pressure vessels used in hydrogen refining applications.
- Weld Overlay: Weld overlays in single or double thickness utilizing GMAW, SAW, and ESW techniques. Enerfab complements weld overlay through our in-house machining capabilities.
- Tube-to-Tubesheet Welding: Enerfab provides specialized tube-to-tubesheet welding heads with the capability for autogenous welding or with filler wire for restraint or strength welds.
- Automated Half-Pipe Welding: We’ve developed a proprietary process for half-pipe jacketing utilizing a continuous coil. This process results in fewer butt joint welds, which means fewer fatigue points, therefore extending the lifespan of your equipment.
-
Our shop floor drawing kiosks enable real-time drawing revisions to your tank and vessel project. No paper on the floor means that only the most updated data is used, minimizing the risk of building off outdated drawings or designs.
From the shop to the field, our investment in the next wave of technology enables us to complete your projects on time and within budget.
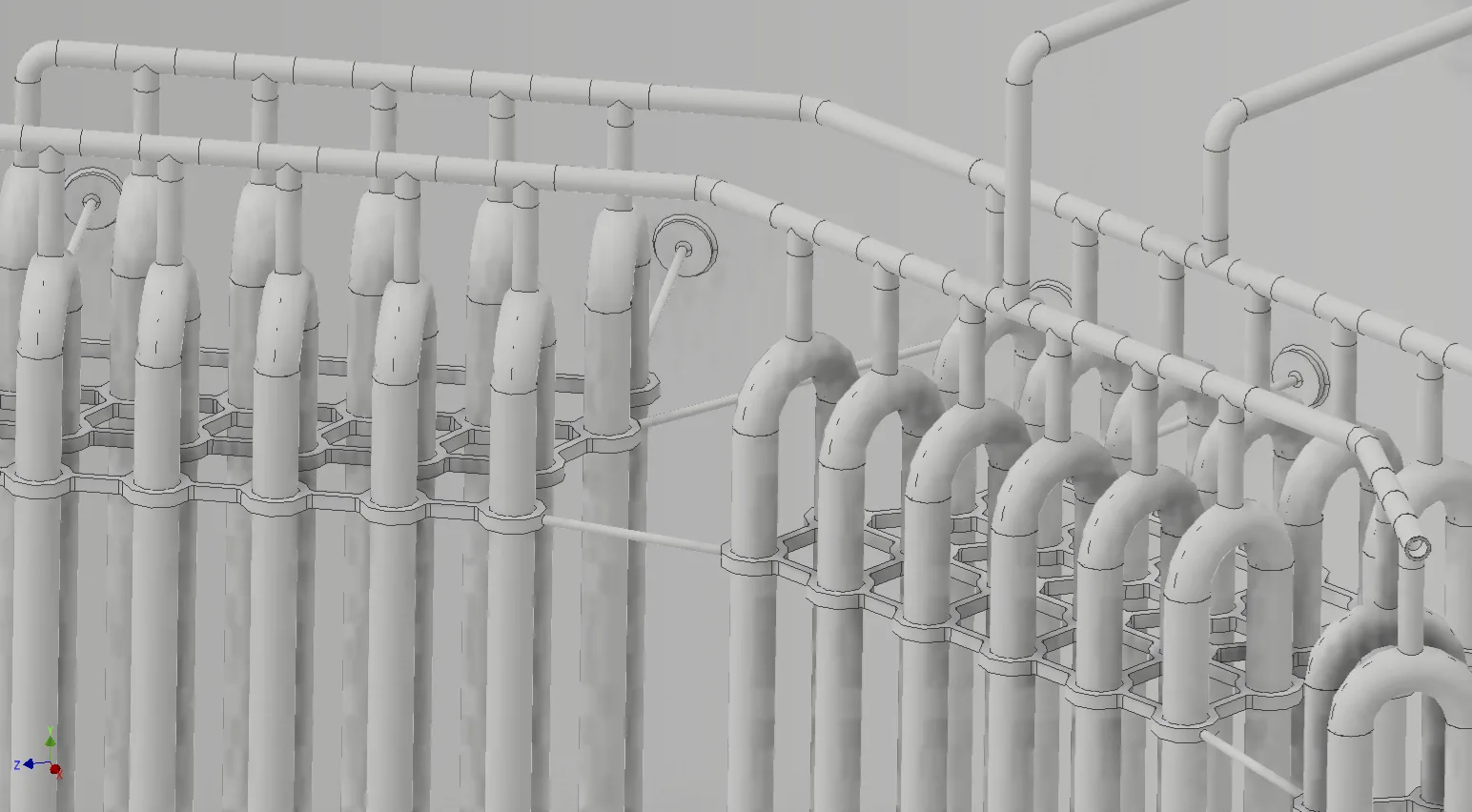
Engineering
Everything we fabricate at Enerfab is done with precision from start to finish. At Enerfab, engineering is not just a department. It is the way we think and how we work. Everything is done with purpose and an engineering mindset, from the estimating phase right through to the delivery and installation of the product.
Enerfab Engineered
Our entire team is trained to have this “engineering” mindset, and our certified engineers serve as the internal guide to ensure every project is completed with excellence, where quality and safety always come first.
This engineered mindset and approach to our work creates a true competitive advantage in the marketplace, combined with our craft knowledge, can-do attitude, labor resources, and multi-shop facilities. No other fabricator can deliver precision and quality quite like Enerfab.
-
With over 70 years of critical process equipment design experience, we have a vast knowledge of industries in addition to pressure vessels, which helps us understand any unique challenge that comes our way. We are real-world engineers who challenge the book and understand that it does not cover what is practical to build. Our cross-trained team enables resource flexibility across all projects. To enhance our expertise, our engineering team is comprised of members of various engineering associations who hold the following credentials and designations:
Members of:
- American Society of Civil Engineers (ASCE)
- American Society of Mechanical Engineers (ASME)
- National Society of Professional Engineers (NSPE)
Credentials & Designations:
- Professional Engineer (PE)
-
Our team follows and complies with the following codes:
- AISC
- API 620
- API 650
- ASCE 7
- ASME
- PIP
- Other unique engineering challenges.
-
Enerfab offers true customer partnerships and wants you to enjoy a positive experience. From concept through completion, we engineer the roadmap and guide you through the process, from bid to installation.
We serve as the guide from concept through completion. Engineering serves as the center of the cog, working with sales, shop, customers, and vendor partners to estimate and deliver the best product possible. We embrace the complex and are proud of the work we do. Engineering doesn’t stop when the drawings are done; we are with you from beginning to end, working with you through every project phase.
We provide transparency and open communication throughout. We assign an engineer and coordinator to each project to verify the objectives, ensure all needs are met, and actively work as the center of communication between internal teams and the customer. Our team will travel to meet with end users 1-on-1 to ensure a complete understanding of the objectives and needs of each project.
If a problem arises, we are the first line of defense in ensuring a solution is found. We will always do what is right. When you turn on a vessel, we want your plant not to worry about the integrity of your process equipment. At the end of the day, our customers’ peace of mind comes from their confidence and trust in us to deliver on our promise of delivering quality projects time and time again.
-
We embrace new technologies and automation to improve the efficiency and quality of our designs. If a system or software doesn’t exist, we will create it. We leverage 3D modeling to minimize the risk of incorrect information and inaccuracies. We can then provide our customers with drawings and designs of their vessel projects with 3D mock-ups of the final product.
We utilize various software to take on more complex configurations. Our in-house proprietary shop floor kiosks enable real-time drawing revisions, creating a paperless atmosphere and ensuring only the most updated data is used to minimize the risk of building off outdated drawings.
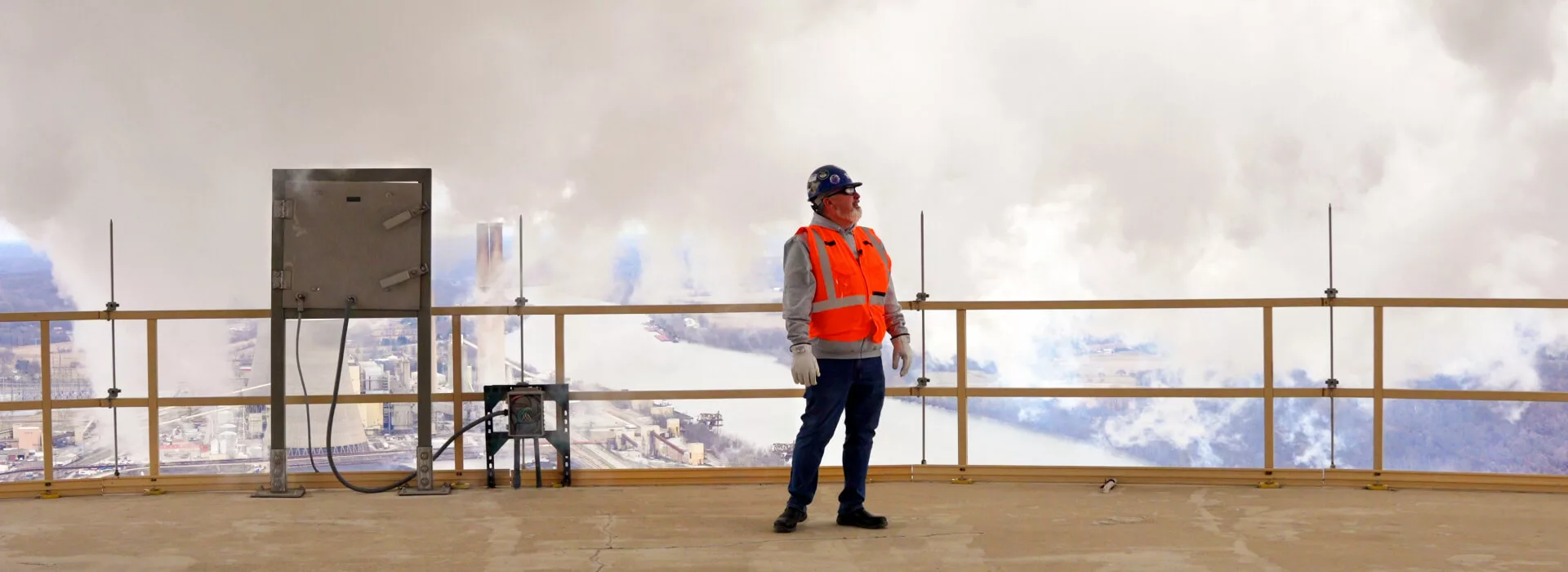
Safety
Sending each of our employees home safely at the end of the day is our most important core value. Simply put, business can’t be achieved without safety at the forefront.
Creating a Safety Culture
Our safety culture resonates through every aspect of our work, from conference rooms to shops and job sites. We keep safety top of mind, every second, every minute, every hour, every day. Safety always.
Additionally, we strive to be a catalyst for improving safety industrywide – that’s why our team members and executive leadership are on the safety committees of various associations and unions. This includes active participation in the boilermakers’ MOST program and the ironworkers’ flagship training program, IMPACT. We equip our team members with Human Performance Improvement (HPI) tools to empower them to speak up for safety, and our OSHA training requirements for each team member exceed industry standards.
HPI Tools
Safety Auditing
Using our digital safety tools, safety managers can proactively monitor safety risks at each of our job sites. This real-time safety auditing application provides easy access to site-specific safety plans, permits, safety records, and other important job site documents at the safety manager’s fingertips. Everyone at Enerfab is responsible for safety.