When Others Say, Heck No, We Say, Let's Go!
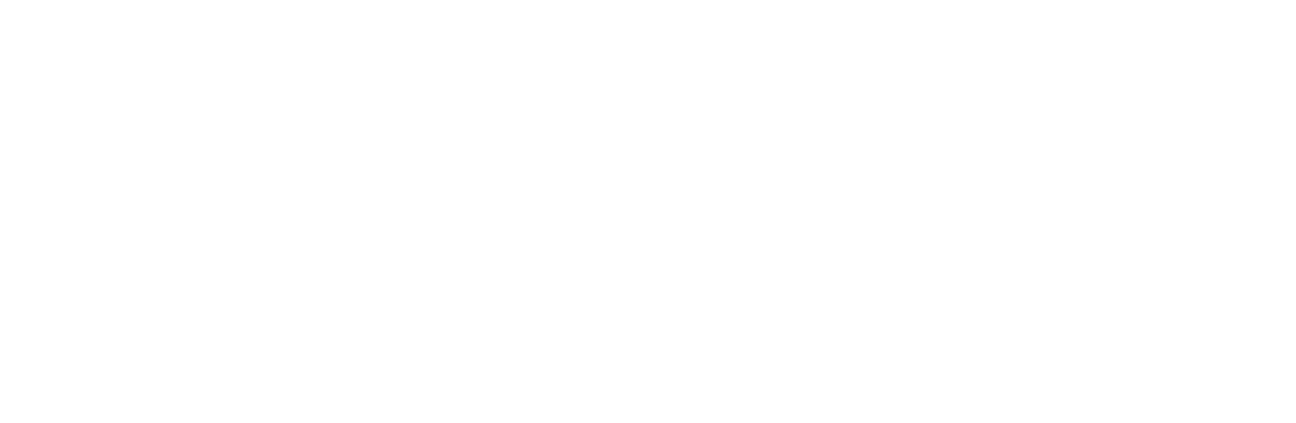
When it hits the fan, we’ve got the plan.
The brutal reality is that your critical process equipment can have unforeseen failures — and in those moments, you need a partner that can get you back up and running as quickly as possible. When our customers (and many of our competitors) say, “Absolutely not! That’s impossible,” about the turnaround times we propose, we say, “Absolutely yes! It is totally possible, and here’s our plan to get it done.”
Get a feel for how we do the seemingly impossible in expedited fabrication in this episode of Building for Real Life, and explore projects we have delivered for customers in record time.
Delivering Rapid Results
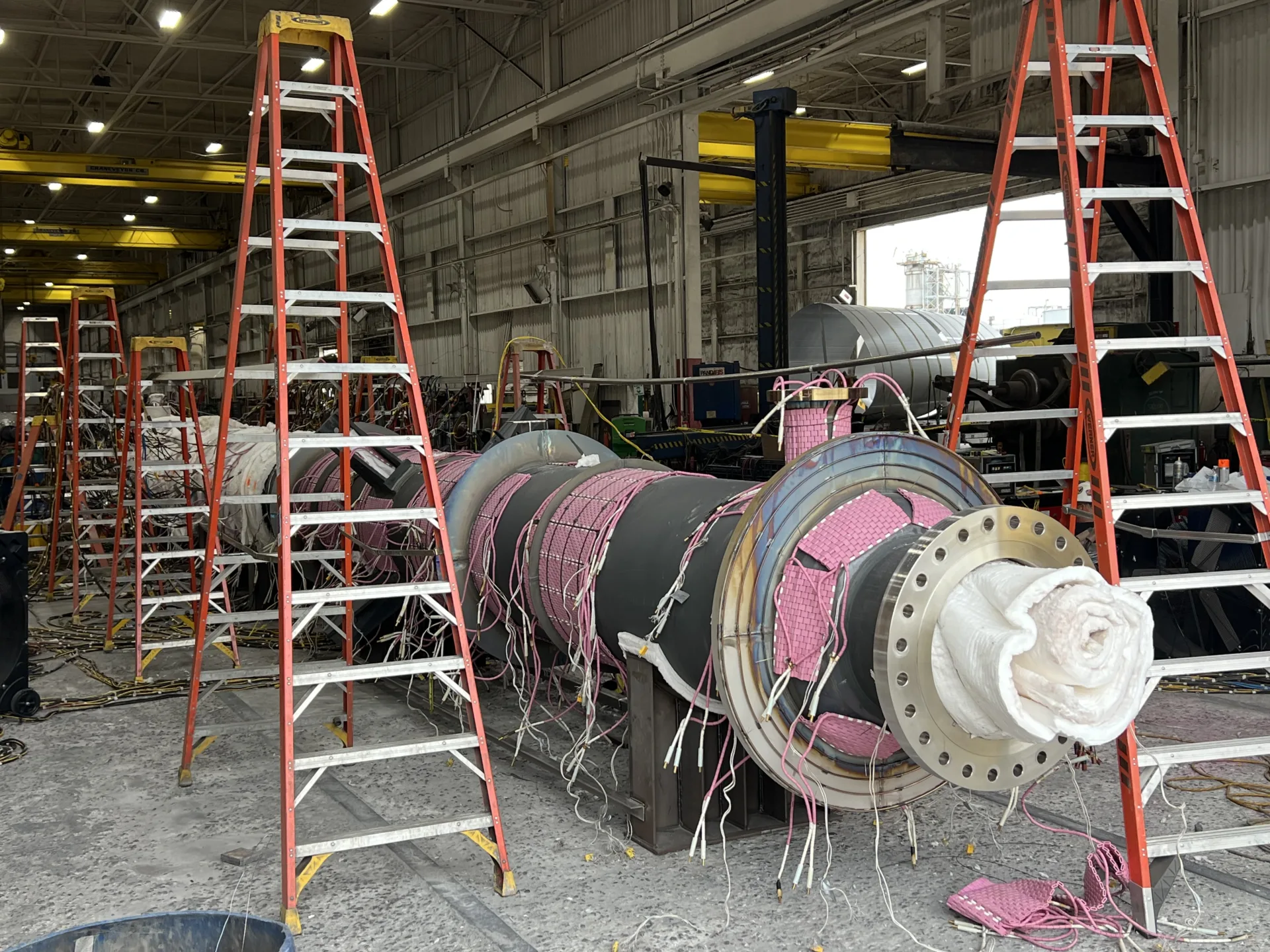
Nickel Alloy Vessels
We delivered 13 of these essential nickel alloy vessels in just 10 weeks.
The project totaled over 1200 linear feet of welding to support our customer’s eco-friendly production process. We solution annealed each piece, and we performed post-weld heat treatment (PWHT) and phased array ultrasonic testing (PAUT).
Refinery Tower
We built this 268′ petrochemical refining tower in just 26 weeks. To accelerate the turnaround, we fabricated the bottom half in Natchez, Mississippi and the top half in Cincinnati, Ohio, before combining the two halves and shipping the tower for installation. See for yourself how it all came together.
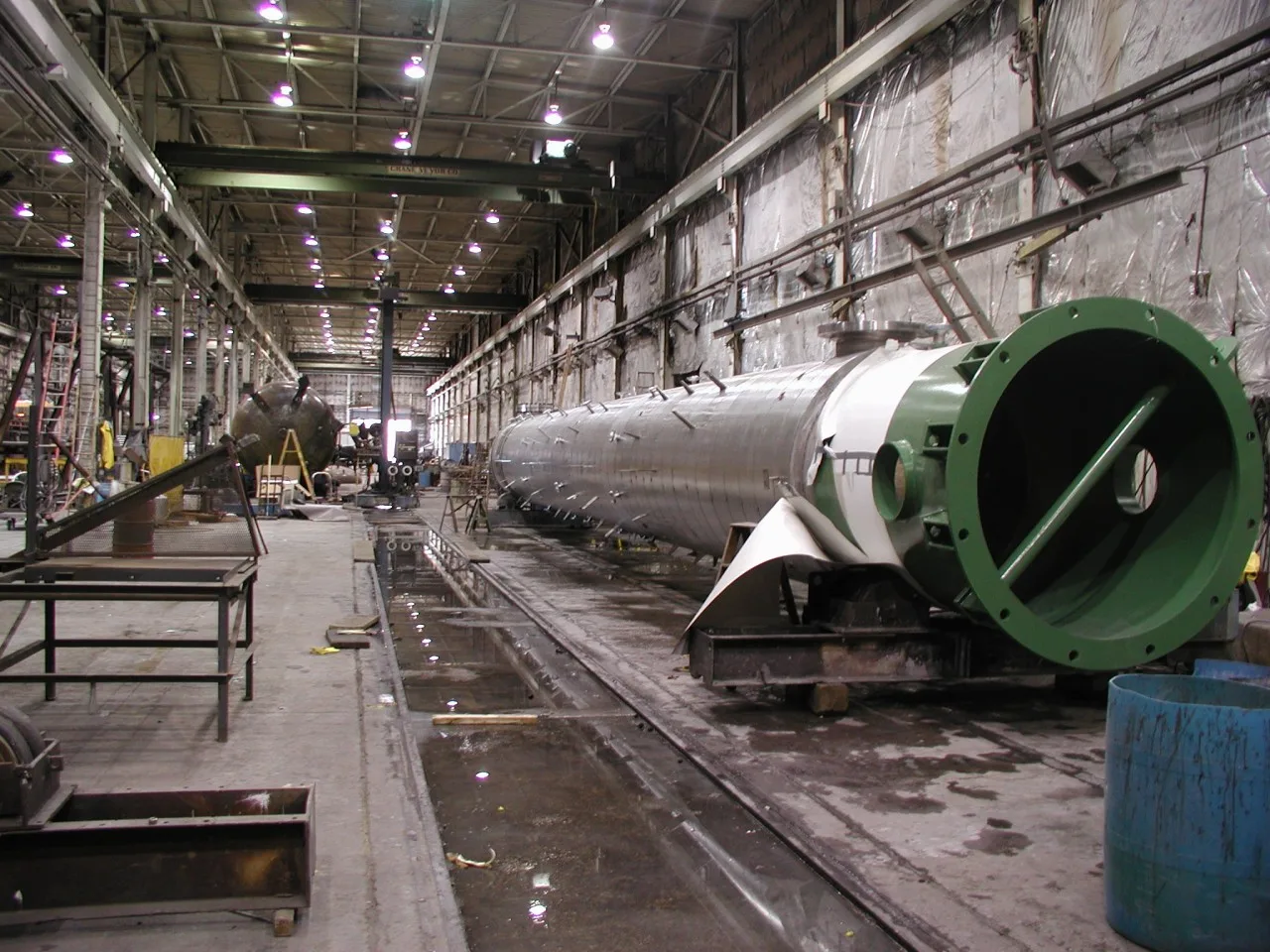
Chemical Distillation Column
We fabricated this column in just 19 days.
Our customer called to replace a column removed from service after discovery during a turnaround. We fabricated this 6′ diameter by 75′ long 316/316L column — with insulation and trial fit of ladders and platforms — in only 19 days. And all of the work was completed in our shop with no need for subcontractors.
Lethal Service Vessel
We delivered this lethal service vessel in 12 weeks.
Our chemical customer called for this 10’x40′ lethal service vessel with platforms. In the three-month project window, we completed engineering, procurement, firm price work, and T&M fabrication.
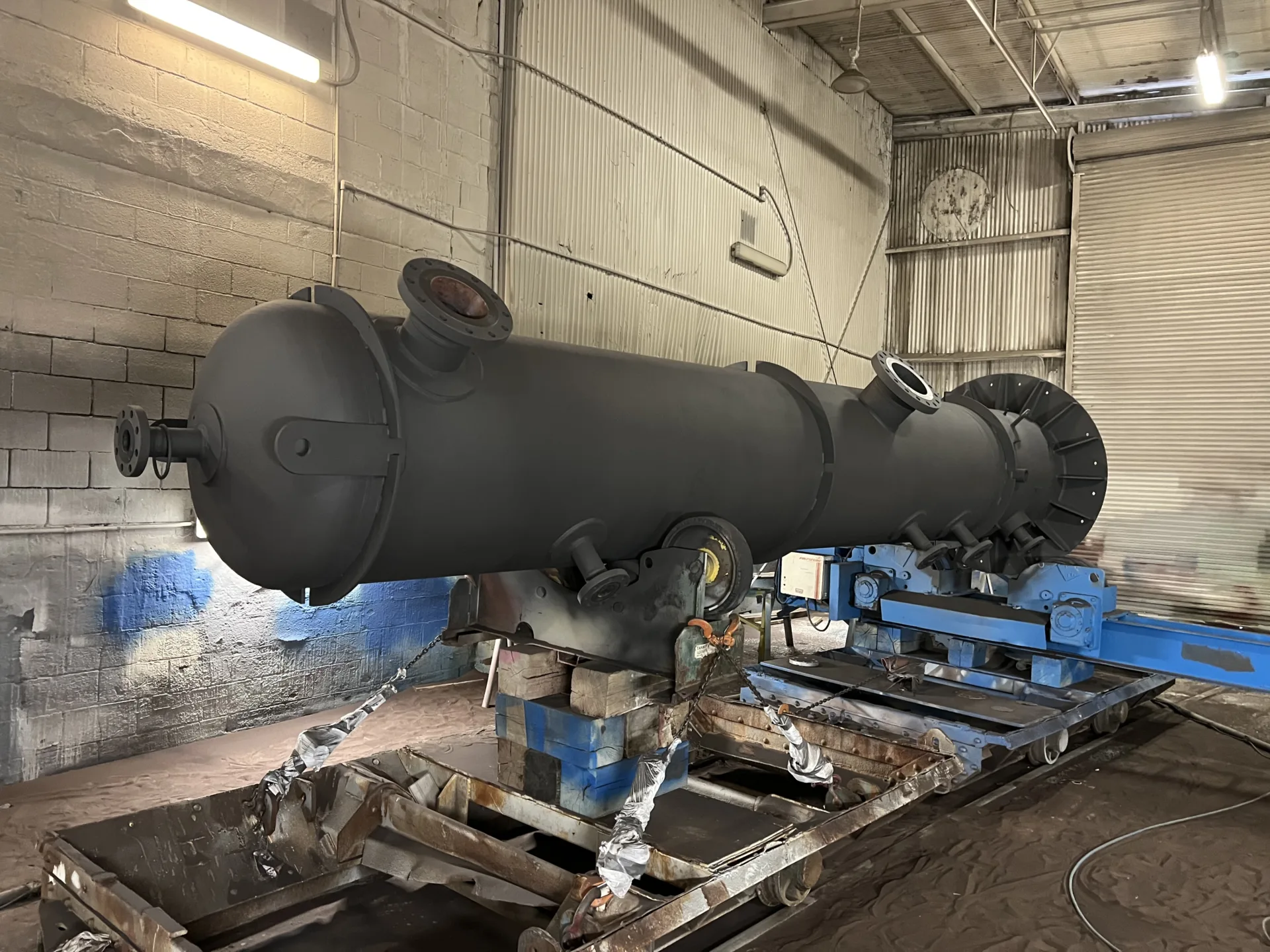
Oil & Gas Condensate Vessel
We fabricated this vessel in 3 weeks.
Our chemical customer needed to replace a code vessel after removing the original from service. This vessel required post-weld heat treatment, hydro testing, and a multi-coat paint system which we completed in three weeks.
Shift Gas Separator
This shift gas separator was completed in 4 weeks.
Our chemical customer needed this critical piece of equipment following an unforeseen catastrophic failure. We fabricated this 2″+ thick, high-pressure alloy vessel, including custom forgings, over the Thanksgiving holiday.
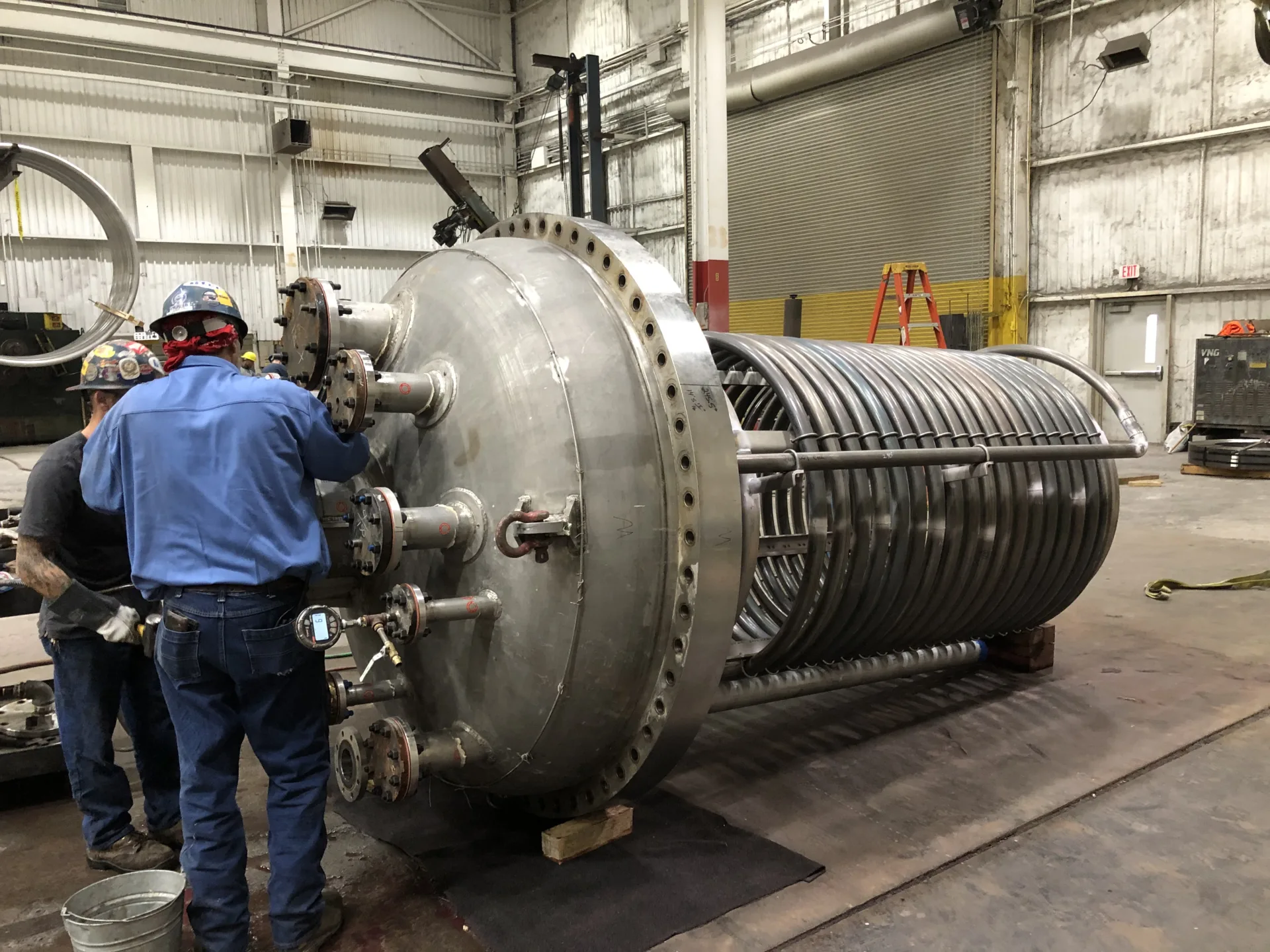
Reactor Rebuild
We rebuilt this reactor in just 10 days.
The rebuild called for new C22 material and included:
- Fabricating the bottom portion of this vessel, including the internal coils
- Fabricating the head and nozzles
- Field repairing the shell and body flange
- Installing a liner plate for damaged overlay
Duplex 2205 Vessels
Three of these Duplex 2205 vessels were built in five weeks.
Our chemical customer needed three Duplex 2205 pressure vessels on skirts to get their process up and running quickly.
The Benefits of Working with Enerfab
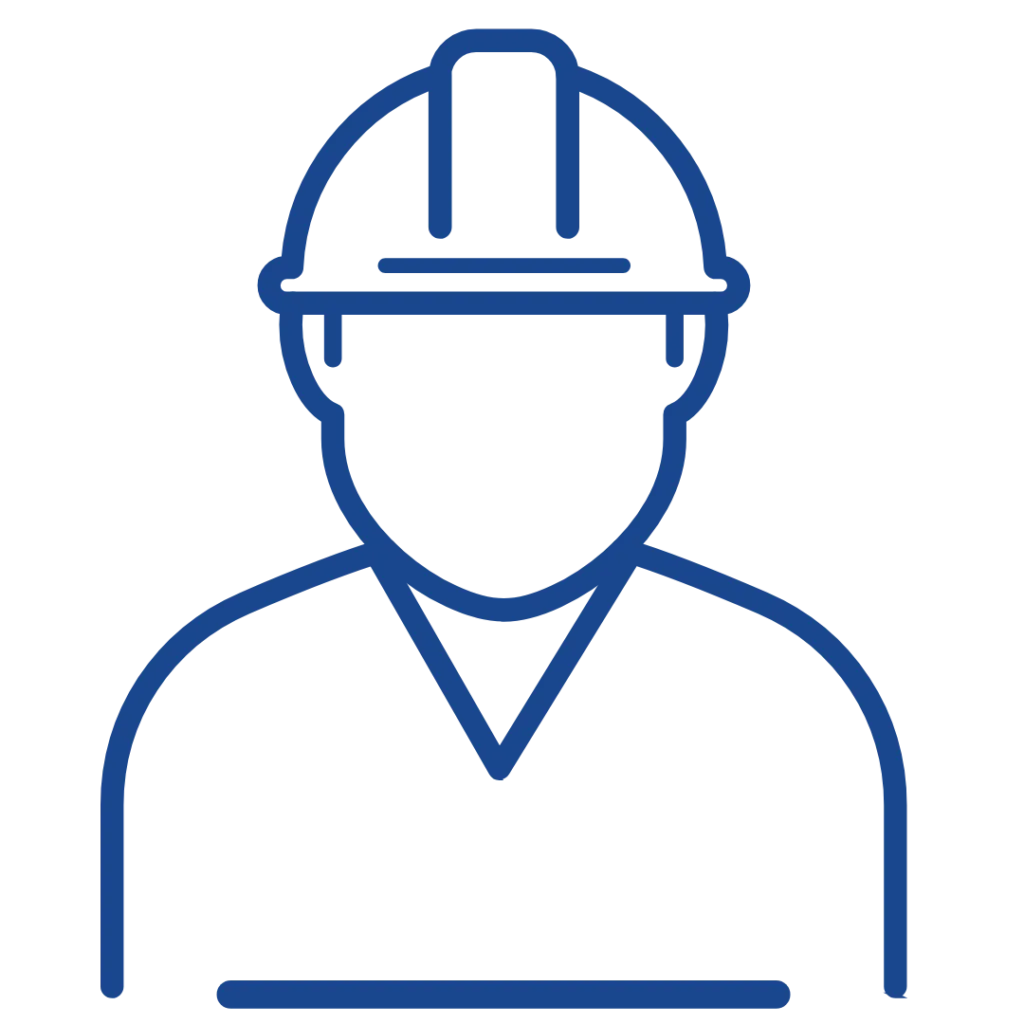
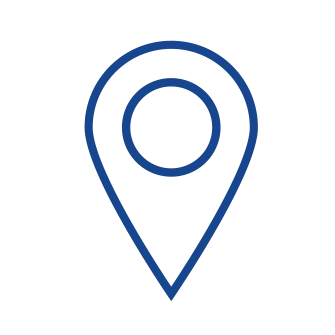
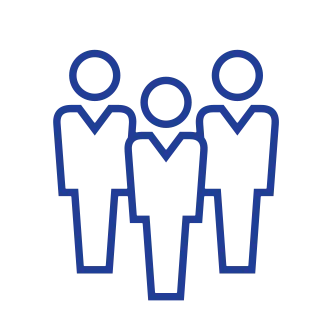
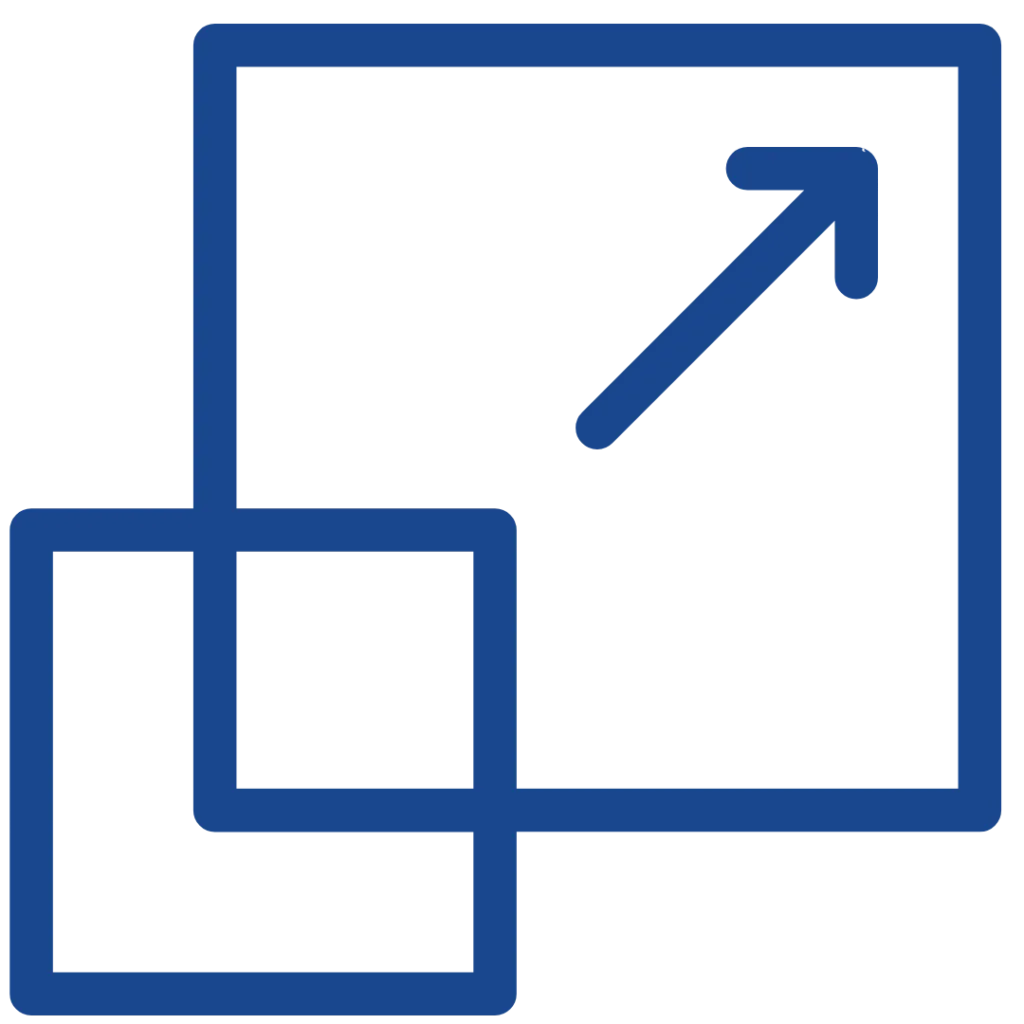