One of Enerfab Process Solutions’s core competencies is the design and fabrication of half-pipe jacketed reactors, commonly used in process industries where temperature control is crucial during chemical reactions. The half-pipe is a type of external jacket that surrounds the reactor vessel and enables the circulation of a temperature-controlling fluid, such as hot water, steam, or cooling water, providing efficient heat transfer and making it suitable for reactions that require precise temperature control.
Quite often, our clients’ processes demand the reactor be operated in a cyclic service where the operating conditions are periodically changed or cycled to facilitate the desired chemical reactions. During cyclic service, the reactor vessel and associated components experience repeated thermal and mechanical stresses as they are subjected to alternating conditions of heating and cooling, which can lead to fatigue, thermal expansion and contraction, material degradation, and other forms of wear and tear over time.
Given the dynamic nature of cyclic service, it is important for chemical reaction vessels designed for such operations to be robust, resistant to corrosion, and capable of withstanding the fatigue stresses associated with thermal cycling. Proper design, material selection, inspection, and maintenance practices are essential to ensure the integrity and reliability of the reactor vessel under cyclic service conditions.
Full-Penetration Welding
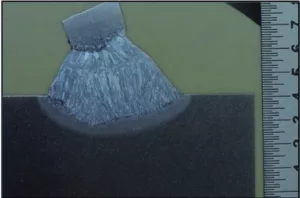
One of the most important aspects in the lifecycle of a half-pipe jacketed vessel in cyclic service is the weld that attaches the half-pipe to the vessel wall. Full-penetration welds provide strong and durable connections but require careful procedures to ensure complete fusion and integrity. In this configuration, the half-pipe jacket is welded to the vessel with full penetration, where the weld extends through the thickness of the jacket wall.
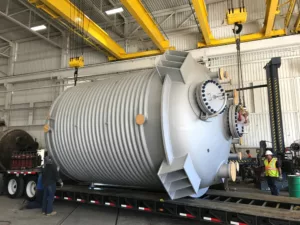
At Enerfab, when we receive a request for a half-pipe jacketed vessel, we first determine if the vessel is going to be operated in cyclical service conditions and which heat transfer medium is going to be used. Often, vessel data sheets or specifications lack these details due to the proprietary nature of the process or other reasons, and more information is required from the client to determine if a standard fillet weld can be used to attach the half-pipe or if full-penetration welding is required. If we see hot oil as the jacket medium or dramatic temperature swings, this can be a red flag that a fillet weld might be problematic during the service life of the vessel.
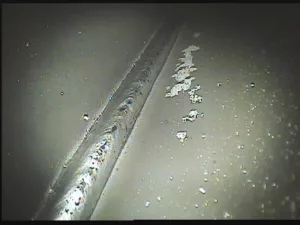
In our experience, the owner’s specifications for welding the half-pipe to the vessel wall vary from no specification to stating the specific weld process, weld procedure, heat input, number of passes, required weld samples and inspection method to be utilized. This variation in details often results in a wide range of pricing from the competitive bidding process. Since full-penetration welding requires more time/labor, we provide an option for a standard fillet weld as well to make sure we are being compared fairly in a bid tabulation. Even when full-penetration welds are specified in a quote request (RFQ), the pricing can still vary due to the interpretation by the fabricators. The desired outcome is a uniform weld on both sides of the half-pipe wall with continuous weld reinforcement and complete fusion. There should not be any stress risers where a potential crack could initiate and propagate during the thermal and pressure cycling of the vessel.
Welding Process Variables
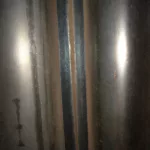
Many different welding procedures, fit-up techniques, equipment automation, and bevels for groove welds are used to achieve the desired full-penetration half-pipe weld by fabricators. The best method will vary depending on a range of factors, such as metal type and thickness. Increasing the initial capital costs for the reactor due to rigorous inspection and specialized welding techniques must be weighed against the long-term cost benefits of a longer service life for the vessel. The best overall value being offered is not very apparent from just a bottom-line number on a bid tabulation.

With the variety of metals and jacket configurations we are involved in, there is no one-size-fits-all solution to half-pipe jacket welding. A submerged arc welding process may be the most efficient and cosmetically pleasing way to lay down a half-pipe attachment weld, but is not the best option for a full-penetration root pass for example. Full-penetration welds may be more suitable for applications prone to fatigue or for heating and cooling media that may contain chlorides. In this case, a GTAW or GMAW root pass may be required due to the arc control and desired heat input to achieve the full-penetration weld. If manual GTAW is utilized, the labor costs will increase, but it will provide one of the most reliable jacket connections to the shell. Automated or mechanized GMAW may be a more economical option. However, the viability of this application is heavily dependent on the shell and half-pipe material type.
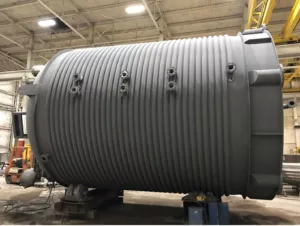
Once the full-penetration welding process is determined, results must be agreed upon between the owner/client and the fabricator. Many times, the best way to do this is with a mock sample. Although this sample is produced in more ideal conditions, it must represent what can be achieved in production. It is important to remember that not all metals “wet” and will flow consistently, so a nickel-based alloy weld will not look as consistent and uniform as a 304, 316, or carbon steel weld. The inspection methods and hold points must also be established before production can begin in the Inspection and Test, Plan (ITP).
Inspection Methods
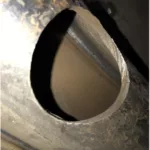
Internal Half-pipe Weld
The typical method for visual inspection of the internal half-pipe weld is to use a borescope camera system, in which the number of linear feet you can inspect is limited by how far the camera can penetrate through the half-pipe coil. Some clients demand 100% visual inspection, which is achieved only by adding inspection ports like the one pictured here or only attaching as much half-pipe to the shell as your camera can visually inspect. The drawback to this is that you either must patch the inspection ports or add couplings which could be problematic later in the service life of the vessel. Additional butt welds are required if you only attach as much half pipe as can be inspected.
Enerfab’s fleet of half-pipe installation machines utilizes continuous coil, which minimizes butt welds. Typically, due to the level of welding automation and our proprietary fit-up technology, what you can see from the borescope through the nozzle inlets and outlets will be representative of the remaining linear feet of the weld.
Want More Insight?
No matter your half-pipe needs, our staff would be happy to discuss your next project and help you obtain the best overall value for your critical process equipment! Learn more about how Enerfab can help you by getting in touch today.