Don’t Worry. We’re Built for the Challenge.
Half-pipe jacketed reactors are typically the workhorse of many chemical synthesis processes. Their operation and design vary considerably in each chemical process. The largest variable is the fabrication, design, and welding by different manufacturers, even if defined by specification. The critical nature of your chemical process operation and the manufacturing technique play a pivotal role in how these reactors should be manufactured and their service life.
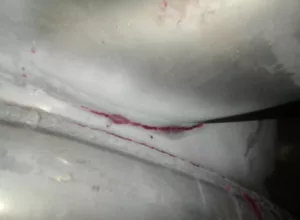

The leading failures in half-pipe reactors are jacket and weld-zone cracks and pinholes. The failure mechanisms may be attributed to corrosion, operation fatigue, improper joint design, and other welding-related factors. These failures can occur in both the base metal, the half-pipe coil, or the weld zone, and are typically attributed to the welded design for the service application. So when it comes to design criteria, one method does not fit all. Enerfab can guide you through this process and offer suggestions to increase performance and reduce plant maintenance.
Enerfab’s Half-pipe Jacketed Reactors and Welding Capabilities
Enerfab’s in-house engineering team will work with you to develop designs that provide the best value based on your facility’s process. So if you have mild temperature excursions and process parameters, we can offer competitive cost solutions to compete with other manufacturers. If your process creates more stress on your critical equipment, Enerfab offers various design and fabrication solutions to engineer your vessel to better meet those performance specifications. And it’s our proven expertise that sets us apart from other manufacturers.
Enerfab utilizes continuous coil from strip to minimize butt welds. Certain butt-weld techniques are usually associated with early half-pipe failures.
Since welding processes vary considerably, selection of the weld process and technique is paramount in obtaining the best metallurgical condition. Our research and experience ensure employee safety and repeatability in our results. Welding automation reduces the potential for defects and variables in man/machine interface and provides the most consistent weld profiles. As a result, Enerfab reactors provide our clients with measurable performance in terms of operation, product yield, and service life!
Reactor Modeling
Occasionally, 2D axisymmetric linear elastic structural analysis may be performed to find stresses for overpressure or fatigue and verify the strength of the half-pipe jacket welded on the shell or head.
Moving to Half-Pipe Design vs. Conventional Jacket
When the annular space dimension is close or equal to half-pipe sizes, and if the jacket pressures do not exceed design parameters, the heat transfer coefficient value is typically higher in half-pipe designs even if internal baffles are used in conventional jacket design. Additionally, higher-value materials, like duplex stainless or nickel alloys, benefit from code allowance to decrease reactor wall thickness and cost. The angle of the coil itself also affects pressure drop characteristics in half-pipe reactors, leading to energy savings, adequate velocities, and turbulence to minimize fouling and improve in heat transfer coefficient responsiveness.
Enerfab Provides:
- Optimized manufacturing processes that solve challenges such as weld cracking and leaks.
- Reduced reactor internal wall waviness due to excessive weld heat.
- Incorporated reactor modeling to determine optimum designs.
- Increased reactor service life in cyclic operations.
- Developed cost-effective designs to meet operational performance applications.
Enerfab Half-Pipe Jacketed Reactors Are Well-Recognized in These Critical Process Segments:
- Monomers
- Fermentation
- Pharmaceutical
- Polymerization
- Polyols
- Hydrogenation
Want more insight?
Let’s talk about the challenges you’re facing with your half-pipe reactors. Learn more about how Enerfab can help you by filling out the form below or contacting us today!